DISCOVER THE SECRETS OF TENNIS STRINGING
Have you ever wondered how tennis and squash strings were made?
Follow this guide !
STEP 1: STRINGING CREATION
In order to understand more about stringing creation, we must first go back to its invention.
This step requires a thorough and complex analysis: understanding the needs of the players to find the product that will help them improve their level of performance or comfort.
Thus, when Tecnifibre invented a new and unique technology in 1983, polyurethane, it revolutionized the market. The "TGV", "NRG²" or "X-One" strings are built around a heart made of synthetic fibers saturated in polyurethane.
It is necessary to get closer to gut strings that these ones have emerged: an assembly of fibers of different materials such as polyamide or polyester is wrapped with a more resistant coat.
The objective: to offer players more comfort and playability, unlike polyester, which is much stiffer and causes injuries to the arms and shoulder for players.

STEP 2: STRINGING FABRICATION
Once the concept is defined, the manufacturing phase begins.
It is therefore necessary to go into the technical considerations, to imagine the necessary materials and the assembly process.
In the case of Tecnifibre, the Cousin Frères factory, resulting from a long industrial tradition of threading, manufactures strings 100% made in France. A leader in the multifilament segment, the factory sets up manufacturing processes according to precise specifications.
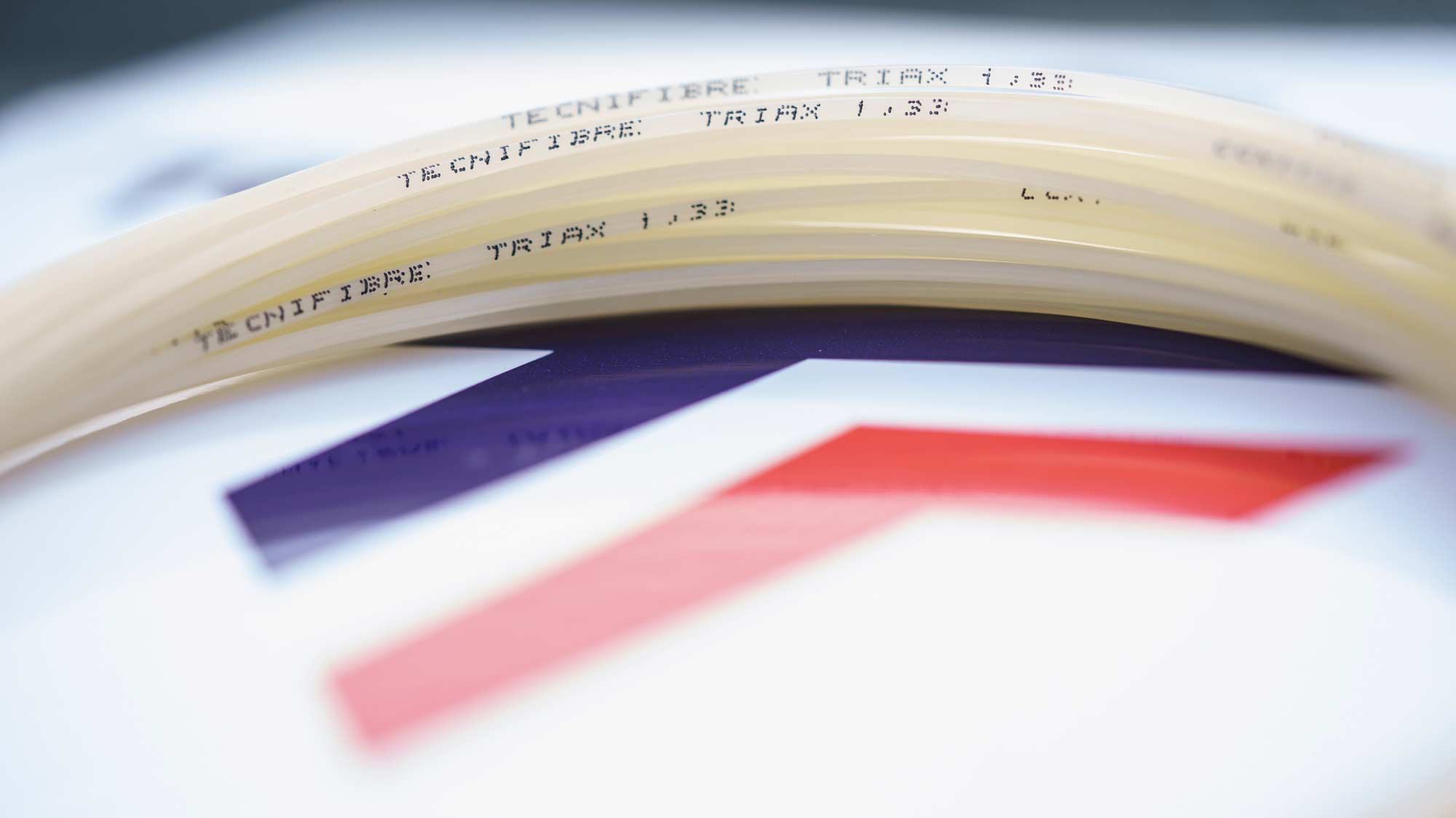
Raw materials are thread and polyurethane. The thread is delivered in large coils whose factory consumes more than 20 tons per year. Then each thread is impregnated individually by the solvent-based polyurethane resin machines. It is possible to mix the fibers in the string (polyamid / polyester), color the resin or play on the twist of the string and the tension of the threads.
The key steps? Solvent removal, polyurethane melting and global smoothing.
The key factors are the raw material, the temperature, the speed of production and the number of turns per meter that we put in the strings (...).
"I think there is a real know-how. We have always wanted to keep control of production. We have many competitors who have outsourced to distant countries; at Tecnifibre, we continue to package our products on site"
Jean-Christophe François
Production Manager
STEP 3: TESTING AND SELLING
Once the string is created, comes the capital time of play testing.
The sample is then adjusted to match the needs of the players and the brand's quality charter.
For this, performance tests are organized externally. For the sensations in play, they are tested by a former professional player whose mission is to push the string to its very limit. Strikes, and more strikes.
These tests are supervised by technical verifications in the laboratory.
"The dynamic tests allow us to get an idea of the dynamic response of a string when put on a racquet" explains Frédéric Salomon, R & D engineer
When all the parties have agreed and the product is perfectly calibrated, then comes the true time of selling it on the markets.
To offer players the best!
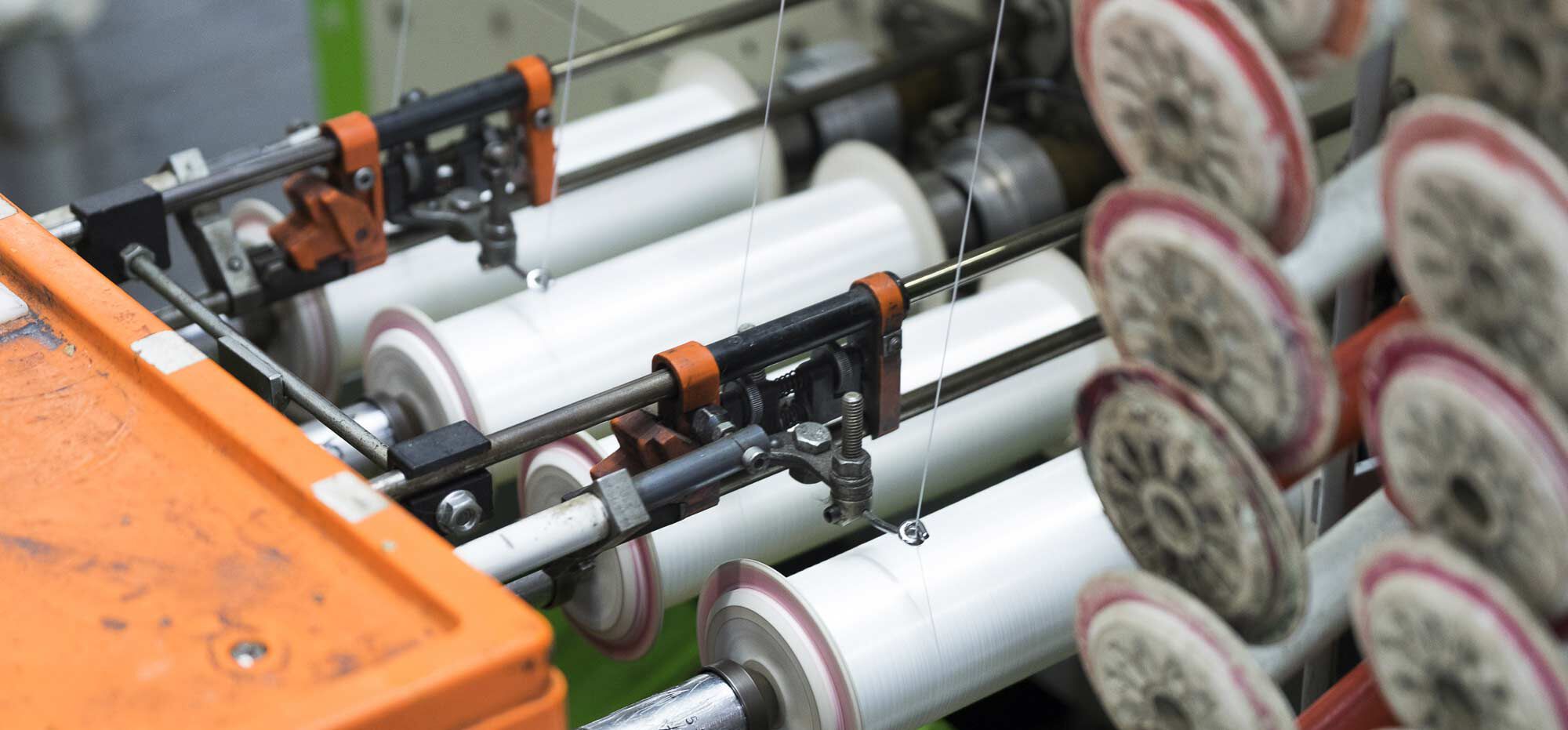